Druckvorstufe
Die ALFT Packaging Company baut in Südasien mit dem KODAK FLEXCEL NX System von Miraclon eine neue Flexo-Größe auf
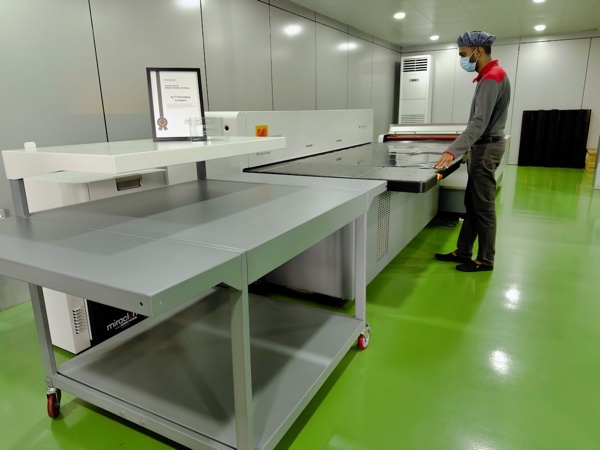
Dienstag 20. Dezember 2022 - Für Lakshman De Fonseka, den Vorsitzenden der ALFT Packaging Company, bedeutete die offizielle Eröffnung des neuen, hochmodernen Verpackungsflexodruckbetriebs in Kotugoda, Sri Lanka, im August eine Rückkehr zu seinen technologischen Wurzeln. Mit der Flexo-Kaschierung stieg Lakshman vor 30 Jahren in die Druckindustrie ein, bevor er ALFT zu einem bedeutenden Verpackungsproduzenten für die Lebensmittelbranche aufbaute.
„Damals war der Tiefdruck das von Markenartiklern aufgrund seiner qualitativ hochwertigen Tonwertwiedergabe bevorzugte Verfahren, also schlugen wir diesen Weg ein und blieben die folgenden 25 Jahre dabei. Aber heute sieht das Ganze anders aus. Was die Qualität betrifft, sehen wir keinen Unterschied zwischen dem Tief- und dem Flexodruck mehr. Das ist fast ausschließlich den Fortschritten in der Plattenbebilderung zu verdanken, welche die FLEXCEL NX Technologie ermöglicht hat. Die neue Produktionsstätte ist ein Zeichen für unser Vertrauen in die Zukunft des Flexodrucks.“
Produktion unter dem eigenen Dach für umfassende Kontrolle
Um die Plattenproduktion ins eigene Unternehmen zu holen, installierte ALFT in dem neuen Werk ein FLEXCEL NX 4260 System, das Platten für eine neue Windmöller & Hölscher Miraflex II-Flexorotation liefert. „Die Investition in die Flexoplattenherstellung und den Flexodruck im eigenen Haus gibt uns die volle Kontrolle und bringt uns zahlreiche Vorteile, die für unsere Kunden von Belang sind“, sagt Lakshman. „Der schnellere Produktionsdurchlauf beim Flexodruck ist ein besonderer Vorteil, der es ermöglicht, Änderungen an Verpackungsdesigns in Bezug auf Farbe oder regionale Varianten zu beschleunigen. Beim Tiefdruck sprechen wir von Vorlaufzeiten von drei bis vier Wochen für Zylinder, die alle importiert werden müssen. Und wenn ein Zylinder während der Produktion beschädigt wird, wartet man zehn bis zwölf Tage auf den Ersatz. Wenn man das mit den 90 Minuten für die Herstellung neuer FLEXCEL NX Platten vergleicht, liegen die Vorteile auf der Hand.“
„Wir können Markenartiklern auch die Vertraulichkeit garantieren, die wichtig ist, wenn sie neue Produkte und Designs auf den Markt bringen. Das kann beim Tiefdruck ein Problem sein, da zwischen der Freigabe der Druckvorlage und dem Eingang der Tiefdruckzylinder viel Zeit vergeht.“
Markenunternehmen begrüßen die Investition in die „beste und neueste Technologie“
An der Eröffnungszeremonie nahmen viele Marken-Kunden von ALFT sowie führende Vertreter der lokalen Wirtschaft und Politik sowie die Technologiepartner von ALFT teil. Hajar Alafifi, die Vorsitzende und Geschäftsführerin von Unilever Sri Lanka, begrüßte die Investition von ALFT in „die beste und neueste Technologie“ und prognostizierte, dass „eine solche Produktionseinrichtung Sri Lanka zu einem erstklassigen Partner für Länder in Süd- und Südostasien machen wird“. Sie beschrieb auch anschaulich, was die Umstellung vom Tiefdruck auf den Flexodruck für alle Markeninhaber bedeutet. „Gegenwärtig müssen wir solche Arbeiten nach Dubai vergeben, was sechs Wochen dauern kann. Da wir das jetzt in Sri Lanka machen können, sind wir agiler, flexibler und schneller auf dem Markt.“
Eine effiziente Produktion ist für ALFT ein zentraler Aspekt. Als das Unternehmen zum Beispiel seinen Tiefdruckbetrieb aufbaute, entsandte es wichtige Mitarbeiter nach Japan, um die dortige Vorgehensweise für eine effiziente Produktion zu studieren. Ihre Erkenntnisse inspirierten ALFT dazu, den gleichen Ansatz zu verfolgen und umzusetzen, was zum Bau einer hochmodernen Produktionsstätte mit strengen Hygiene- und Reinigungsstandards führte. Dies ermöglichte es ALFT auch, der einzige Verpackungsproduzent in Sri Lanka zu werden, der bei der BRC Global Food Safety Standards-Zertifizierung mit A+ bewertet wurde.
Besonders wichtig ist, wie sich die FLEXCEL NX Platten im Druck verhalten. „Die Konsistenz der Platten bedeutet, dass wir den Produktionsprozess standardisieren und die neue Druckmaschine mit maximaler Effizienz und Produktivität betreiben können. Dies ermöglicht uns auch, für bestimmte Marken im erweiterten Farbraum (ECG) zu drucken, was ein zusätzlicher gewaltiger Effizienzgewinn ist. Außerdem sind FLEXCEL NX Platten sehr haltbar, sodass wir weniger Maschinenstopps haben.“
„Immer das Produkt Nummer eins wählen“
Lakshman ist erfreut, dass seine frühe Begeisterung für den Flexodruck inzwischen bestätigt wurde und die Technologie weithin als hochwertiges Produktionsverfahren für flexible Verpackungen anerkannt ist. Er schreibt diesen Wandel dem FLEXCEL NX System zu: „Das grundlegende Konzept und die Bauweise einer Zentralzylinder-Flexodruckmaschine haben sich nicht verändert. Was sich geändert hat, sind die Druckvorstufe und die Druckformherstellung im Vorfeld der Druckmaschine, und diese Entwicklung wurde von den Rasterwalzen- und Druckfarbenherstellern unterstützt. Jetzt ist also alles auf dem richtigen Niveau und geht in die richtige Richtung.“
Auf die Frage, warum sich ALFT für das FLEXCEL NX System entschieden hat, sagt er schlicht: „Das FLEXCEL NX System ist eine hervorragende Produktionslösung“ und fügt hinzu: „Unsere Philosophie ist es, immer das Beste zu kaufen. Wenn man sich für eine andere Lösung als die Nummer eins entscheidet, geht man Kompromisse ein und kann nicht das Beste aus dem Ganzen herausholen. Aus diesem Grund haben wir in die W&H Miraflex II und das FLEXCEL NX System investiert. Sie gehören zum Besten, was an Produktionstechnik für die Flexodruckbranche verfügbar ist. Sie arbeiten wunderbar zusammen, gewährleisten schnelle Auftragswechsel und ermöglichen kürzere Durchlaufzeiten.“
Umstellung vom Tief- auf den Flexodruck
Lakshman räumt zwar ein, dass der Tiefdruck auf den süd- und südostasiatischen Märkten noch immer das dominierende Verfahren ist, doch sieht er für die Zukunft eine stetige Abwanderung von Aufträgen zum Flexodruck voraus. „Es geht einfach darum, die Einstellung der Kunden zu ändern, und das funktioniert am besten, wenn man ihnen die Ergebnisse präsentiert. Daher verlagern wir nach und nach Arbeiten, die bislang im Tiefdruck produziert wurden, in den Flexodruck – natürlich mit dem Einverständnis unserer Kunden. Wir gehen dabei so vor, dass wir bei jeder Änderung an einem Produkt die Gelegenheit nutzen, eine Flexo-Version vorzuschlagen. Nach unserer Erfahrung sind die Markenunternehmen mit dem Wechsel sehr zufrieden, wenn wir ihnen zeigen können, dass die Qualität des Flexodrucks der des Tiefdrucks ebenbürtig ist. Insbesondere, wenn sie all die zusätzlichen Effizienzvorteile erhalten, die der Flexodruck mit sich bringt.“