Offsetdruck
Beste Voraussetzungen für „traditionell erstklassigen“ Druck
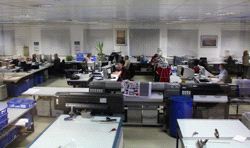
Montag 06. Juli 2009 - Rollenoffsetdruck als Kerngeschäft, eine hoch professionelle, standardisierte Produktion sowie die Realisierung von Wachstum durch permanente Erweiterung der Wertschöpfung sind wichtige Eckpfeiler der Strategie von Evers-Druck. Die Automatisierung der internen Druckvorstufenprozesse mit dem KODAK PRINERGY Workflow System liegt ebenso auf dieser Linie wie die effiziente Online-Zusammenarbeit mit Kunden über das webbasierte KODAK INSITE Prepress Portal System und die prozessstabile CTP-Produktion mit Thermoplattenbelichtern von Kodak.
Die im schleswig-holsteinischen Meldorf beheimatete Evers-Druck GmbH agiert am Markt als vollstufiger Druckdienstleister mit großer Wertschöpfungstiefe. Das Attribut „vollstufig“ kann im konkreten Fall sehr großzügig ausgelegt werden. Denn einerseits beginnt die Kompetenz im produktionsvorgelagerten Bereich schon bei der Konzeption und Realisierung von Database-Publishing-Projekten oder der kompletten Prepress-Bearbeitung von Katalogen einschließlich kreative Bildbearbeitung. Andererseits verfügt das Unternehmen am Ende der grafischen Produktionskette über eine schlagkräftige, kapazitätsstarke Druckweiterverarbeitung und Logistik.
Reise- und Versandhauskataloge, Imagebroschüren und Zeitschriften (Verlagsobjekte, Kundenmagazine) machen rund 90 % des Geschäfts von Evers-Druck aus. In dem PSO- bzw. ISO-12647-2-zertifizierten Betrieb beherrscht der Rollenoffset das drucktechnische Geschehen. Zehn Heatset-Rotationen decken ein breites Formatspektrum ab, von acht Seiten im liegenden Format über 16, 32 und 40 Seiten bis zu 80 Seiten stehend im Magazinformat. In die 80-Seiten-Klasse ist Evers-Druck erst vor Kurzem vorgestoßen, nachdem umfangreichere Aufträge gewonnen werden konnten, die sich alleine schon aus Zeitgründen nicht auf mehrere Druckmaschinen verteilen lassen. Der Bogenoffsetdruck ist in Meldorf durch zwei Maschinen im 3B-Format mit diversen Möglichkeiten der Inline-Lackveredelung vertreten, hauptsächlich für die Produktion von Umschlägen und Ergänzungsprodukten wie Postkarten etc.
Die Format- und Maschinenvielfalt schafft flexible Möglichkeiten zur wirtschaftlichen Gesamtherstellung von Druckobjekten mit stark variierenden Seitenumfängen und Auflagenhöhen. Aus dieser Vielfalt resultieren aber auch besondere Anforderungen an die Druckvorstufe. „Wir setzen in allen Bereichen auf Standardisierung und Integration. Das beginnt schon in der Auftragskalkulation und zieht sich durch alle Produktionsbereiche bis in die Logistik. So erhalten wir überall transparente und effiziente Prozesse“, sagt Matthias Langenohl, Bereichsleiter Technik.
Ganz im Sinne dieser Strategie ist das KODAK PRINERGY Connect Workflow System der Druckvorstufe mit dem Produktions- und Steuerungssystem printnet vernetzt, beispielsweise für Job-Status-Meldungen und die Übergabe von Farbzonen-Voreinstelldaten. In puncto Hardware wurde das Workflow-System auf eine hohe Belastung und ununterbrochenen Betrieb ausgelegt. Ein Primär- und zwei Sekundärserver sowie drei Renderstations, welche die Daten für die Ausgabesysteme generieren, bilden das hardwaretechnische Rückgrat des Prepress-Workflows von Kodak. Ein weiterer Server ist dem KODAK INSITE Prepress Portal System vorbehalten.
Prepress-Workflow: Hohe Verarbeitungskapazität, gepaart mit individueller Automatisierung
Bis zu 1.600 Farbseiten hat die Druckvorstufe täglich zu verarbeiten. Angesichts dieser Größenordnung leuchtet es ein, dass Matthias Langenohl den hohen Stellenwert automatisierter Abläufe betont: „Wir können uns nicht um jede Seite im Einzelnen kümmern, sondern brauchen schon beim Dateneingang zuverlässige automatische Prüfroutinen. Eventuelle Probleme müssen möglichst früh aufgedeckt werden, damit wir Folgekosten vermeiden und mit den heutigen engen Zeitfenstern zurechtkommen.“ Etwa 90 % der Seiten kommen bei Evers-Druck als fertige PDF-Dateien an. Vor der Verarbeitung durch den Prepress-Workflow durchlaufen die PDFs komplexe automatische Preflight-Kontrollroutinen.
Was den Datentransfer und die Zusammenarbeit mit in- und ausländischen Kunden betrifft, spielt das KODAK INSITE Prepress Portal System eine tragende Rolle. Es überbrückt geografische Distanzen und sorgt bei engen Terminen für Entspannung. Rund 600 Auftraggeber nutzen mittlerweile das webbasierte Portal, das unmittelbar mit dem PRINERGY Workflow System verknüpft ist, zur Übermittlung ihrer Dateien in die Evers-Druckvorstufe und für Online-Korrektursitzungen. Wie Vorstufenleiter Klaus Gromoll bemerkt, hat die erhöhte Benutzerfreundlichkeit in Form blätterbarer Seiten die Akzeptanz des INSITE Prepress Portal Systems im Kundenkreis gesteigert.
Ob es um die Überprüfung eingegangener Dateien, die Ausgabe farbverbindlicher Proofs, das Erstellen der Ausschießer oder die Ausgabe von Formproofs geht, die Regelbasierte Automatisierung (RBA) des PRINERGY Workflow Systems nimmt dem Druckvorstufenpersonal eine Fülle von Routineaufgaben ab und sorgt dafür, dass die Daten in die richtigen Bahnen gelenkt werden. „Die RBA bietet uns den Vorteil, dass wir selbst die Abläufe nicht nur auf dem Papier standardisieren, sondern im Workflow-System feste Regeln nach unseren eigenen Anforderungen aufstellen können. Das führt zu einer höheren Prozesssicherheit“, berichtet Matthias Langenohl.
So kann der RBA-gesteuerte Workflow Dateien selbsttätig an Fremdsysteme, z. B. für die Farbproofausgabe, übergeben, wenn bestimmte Bedingungen erfüllt sind. Ebenso kann die RBA, sobald beispielsweise die Seiten einer Signatur (Schön- und Widerdruckform) vollständig verarbeitet sind, automatisch die Digital Blueline-Funktion des Workflow-Systems aktivieren. Digital Blueline stellt die Seiten eines Jobs automatisch in Zweier- oder Vierergruppen in der normalen Lesereihenfolge zusammen, um auf schnellen Farblaserdruckern ausgegeben zu werden. So lassen sich ohne großen Aufwand Handmuster anfertigen, die entweder hausintern überprüft oder den Kunden für die endgültige Druckfreigabe zugesandt werden, bevor die Platten hergestellt werden.
CTP für die industrielle Druckproduktion
Bei Evers-Druck trägt ein voll automatisierter KODAK MAGNUS VLF QUANTUM Plattenbelichter die Hauptlast der digitalen Druckplattenbebilderung. Es handelt sich um die besonders produktive X-Geschwindigkeitsversion. Eine vorgeschaltete Mehrkassetteneinheit (MCU) beschickt den Plattenbelichter vollautomatisch mit Druckplatten in unterschiedlichen Formaten. Das im August 2008 in Betrieb genommene Großformat-CTP-System wird von zwei älteren KODAK TRENDSETTER VLF Plattenbelichtern flankiert, die heute in erster Linie als Backup-Systeme die Produktion absichern.
Das Unternehmen hat seine Druckformherstellung schon ab Mitte der 1990er-Jahre auf Computer-to-Plate umgestellt und mit verschiedenen Systemgenerationen und Bebilderungstechnologien Erfahrungen gesammelt. „Aber erst die großformatigen TRENDSETTER Plattenbelichter haben mit der KODAK SQUARESPOT Thermobebilderungstechnologie die Ruhe und stabilen Verhältnisse in der Plattenherstellung etabliert, die wir uns von CTP immer erhofften“, sagt Klaus Gromoll.
Deshalb war es eine folgerichtige Entscheidung, bei der erneuten CTP-Investition wieder auf die Reproduzierbarkeit und Präzision der SQUARESPOT Technologie zu setzen, wobei der MAGNUS VLF QUANTUM Plattenbelichter auch die nötige hohe Durchsatzkapazität mit sich brachte. Mit Inbetriebnahme dieses CTP-Systems stellte Evers-Druck die ganze Druckformherstellung auf die KODAK ELECTRA EXCEL HRO Platte um, die für alle Produktionsarten eingebrannt wird. Aufgrund ihrer hohen Auflösung und der Fähigkeit, bei sehr feinen Rastern einen breiten Tonwertumfang zu übertragen, ist die vorerwärmungsfreie Thermoplatte wie gemacht für das differenzierte Anforderungsprofil von Evers-Druck in Sachen Rasterung. Neben dem klassischen AM-Raster und der FM-Rasterung mit der KODAK STACCATO Rasterung kommt das Unternehmen besonderen Kundenwünschen mit dem Angebot weiterer Rasterverfahren bzw. -varianten entgegen.
Forderungen aus dem Markt nach einer „Detailauflösung von FM ohne Produktion mit FM“ veranlassten das Team um Klaus Gromoll u. a. zu Tests mit Hybridrastern. Die KODAK MAXTONE Rasterung kristallisierte sich als ideale Lösung für solche Fälle heraus. Diesem AM-Hybridraster liegt eine konventionelle AM-Rasterstruktur zugrunde, wobei die Tonwerte in den extremen Lichter- und Tiefenbereichen wie bei FM-Rastern durch die Variation der Punktverteilung gesteuert werden. Dies ermöglicht den Einsatz von sehr feinen Rastern – z. B. 96/cm mit 20- bis 30 µm-Hochlichtpunkten – und lange unterbrechungsfreie Produktionszyklen im Hochauflagendruck. Für die standardisierte Produktion mit diesen wie auch weiteren Raster-Finessen, so etwa der Kombination von AM- und der FM-Rasterung in einem Farbsatz, ist man in Meldorf mit der Workflow-, CTP- und Plattentechnologie bestens gerüstet.