Verpackung
Entscheidend ist der Gesamtprozess: Integrierte Live-Verpackungsproduktion im Print Media Center
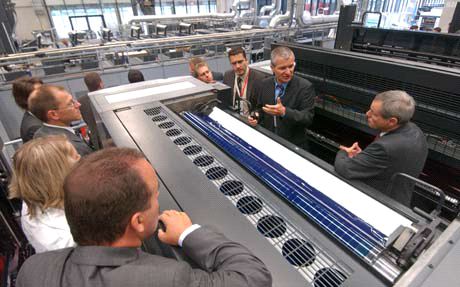
Mittwoch 22. Juli 2009 - Mittendrin statt nur dabei sind die Gäste des Print Media Centers (PMC), wenn dort Druckjobs kalkuliert, angelegt, gedruckt, gestanzt und geklebt werden. Seit Beginn der Kundendemos in der Halle 11 am Standort Wiesloch-Walldorf der Heidelberger Druckmaschinen AG (Heidelberg) im November 2008 haben dort bereits rund 600 Gäste aus der ganzen Welt Lösungen von Heidelberg für den Verpackungs- und Etikettendruck live erlebt. Mit über 4.000 Quadratmetern ist das PMC das weltweit größte Kompetenzzentrum seiner Art. Es zeigt eine Produktionsumgebung mit drei vollständigen Produktionslinien inklusive integriertem Workflow und jede Vorführung kann auf die individuellen Bedürfnisse und Interessen des Gastes zugeschnitten werden.
Wir sind uns bewusst, unter welchem Druck die Verpackungsbranche steht. Im internationalen Wettbewerb müssen jedes Jahr Produktivitätszuwächse von 3 bis 5 Prozent erzielt werden, erklärt Dr. Jürgen Rautert, Vorstand Produkte und Vertrieb der Heidelberger Druckmaschinen AG. Wir sind in engem Kontakt mit großen und kleinen Betrieben der Verpackungsbranche und entwickeln unser Portfolio auf Basis der gemeinsam erarbeiteten Anforderungen ständig weiter. Die Strategie von Heidelberg ist klar: Lösungen für den wenig zyklischen Verpackungsdruckmarkt sollen künftig 25 Prozent des Gesamtumsatzes des Unternehmens ausmachen.
Erfolgsfaktoren für den Verpackungsdruck
Wo liegen nun die Vorteile einer integrierten Verpackungsproduktion für den Kunden und wie können sich Interessenten unter Praxisbedingungen im PMC von der Eignung der Heidelberg Lösungen für künftige Investitionen überzeugen?
Gläserne Produktion
In der Produktion sind Jobstatus und eingesetzte Ressourcen jederzeit abrufbar. Die Maschinen CTP-Belichter, Druckmaschinen, Stanzen oder Faltschachtelklebemaschinen sind über einen Prinect Workflow verbunden und liefern Betriebsdaten in Echtzeit. Damit werden Produktions- und Ausfallzeiten automatisiert für jeden Auftrag erfasst. Diese Ergebnisse werden für eine exakte Nachkalkulation herangezogen und fließen außerdem in den Erfahrungsschatz des Systems ein. So werden künftige Angebotskalkulationen immer exakter. Nur wer seine Produktionsdaten genau kennt, kann die Prozesse optimieren und die Effizienz steigern. Prinect liefert dazu alle wichtigen Informationen. Genau diese Vorteile der Prozesstransparenz erleben die Gäste im Print Media Center gerne auch anhand eigener Druck- und Verpackungsjobs.
Höhere Produktionssicherheit und Datenqualität
In einem integrierten Produktionsprozess erfolgt die Eingabe der Auftrags- und Produktionsdaten pro Job nur einmal an zentraler Stelle in der Arbeitsvorbereitung. Jeder Produktionsschritt Vorstufe und Druck ebenso wie Stanzen und Faltschachtelkleben greift automatisch auf diese Ursprungsdaten zu und fügt automatisch weitere Daten hinzu, die sich aus dem Prozess ergeben. Den folgenden Prozessschritten stehen diese Daten sofort zur Verfügung. Sicherheit in allen Produktionsprozessen ist die entscheidende Voraussetzung für eine rentable Verpackungsproduktion individuelle Bedienungsfehler lassen sich damit ebenso vermeiden wie inkonsistente Daten in den einzelnen Prozessschritten. Bei Wiederholaufträgen stehen alle Parameter des Vorgängerauftrags zur Verfügung, so dass die Produktion in kürzester Zeit und mit gleicher Fertigungsqualität anlaufen kann wichtige Faktoren für den wirtschaftlichen Erfolg des Verpackungsdruckers.
Planung in Echtzeit
Wie gelingt es mir, den gerade eingetroffenen Expressjob meines Stammkunden noch pünktlich zu produzieren und auszuliefern? Antworten darauf sehen die Besucher des PMC anhand der elektronischen Plantafel. Sie zeigt Abweichungen von der Planung direkt an und ermöglicht sofortige Reaktionen, um alle Termine einzuhalten. Auf diesem Wege lassen sich auch kurzfristige Kundenanfragen einplanen, und zwar ohne andere Aufträge zu gefährden. Die elektronische Produktionsplanung entlastet damit Disponenten und reduziert zudem Produktionszeiten, indem sie einen bisher nicht möglichen Umfang an Echtzeitinformationen über die Produktion sowie flexible Planungshilfen zur Verfügung stellt. So lassen sich zur Produktionsoptimierung beispielsweise mehrere Druckaufträge mit gleichen Sonderfarben zusammen einplanen, um Rüstzeiten zu reduzieren. Vorreservierungen von Maschinen für bestimmte Aufträge können eingetragen werden und die Auswirkungen auf die Gesamtplanung werden sofort an allen Arbeitsstationen sichtbar.
Offenheit des Systems
Je nach Größe und Anforderungen eines Verpackungsdruckers lassen sich unterschiedliche ERP- (Enterprise Resource Planning) oder Management-Informationssysteme über eine Standardschnittstelle in den Prinect Workflow einbinden, zum Beispiel LP. Packaging eine SAP-Lösung von Dr. Lauterbach und Partner, Boxsoft von CSG oder Prinance. Daten aus CAD-Systemen und Grafikprogrammen können ebenfalls in den Prinect Workflow übernommen werden. Das System ist vollkommen modular konfigurierbar und passt sich an die individuellen Gegebenheiten der Druckerei an. Natürlich können auch bereits existierende Produkte beim Kunden eingebunden werden.
Höchste Verfügbarkeit
Eine kontinuierlich stabile und sichere Produktion ist oberstes Gebot nicht nur im Verpackungsdruck. Der Heidelberg Service stellt die Verfügbarkeit der Maschinen und damit die Produktivität sicher, die Zahl ungeplanter Ausfälle wird auf ein Minimum reduziert. Hierzu zwei Beispiele:
Beim Heidelberg Remote Service kann ein Service-Techniker per Internet auf die Maschine zugreifen, Diagnosen stellen und Fehler binnen Minuten beheben.
Erhebliche Zeit und Kosten spart auch die neueste Service-Option eCall. Dabei meldet sich die Maschine im Falle einer Störung automatisch beim Heidelberg Service. Erfolgt die Zustimmung durch den Anwender, wird ein Fehlerticket eröffnet. Früher vergingen rund 30 Minuten zwischen einer Fehlermeldung und dem Anlaufen der Problemlösung. eCall reduziert diese Zeitspanne auf weniger als eine Minute. Zusätzlich können aufgrund der wesentlich qualifizierteren Daten bis zu 70 Prozent der Fälle bereits beim ersten telefonischen Kontakt zwischen Serviceexperten und Maschinenbediener gelöst werden.
Verpackungsproduktion im PMC: Schritt für Schritt von Station zu Station
Da die Heidelberg Lösungen sowohl im Verpackungsdruck als auch im klassischen Akzidenzdruck einsetzbar sind, stehen umgekehrt alle bekannten Vorteile der Heidelberg Produkte in integrierten Gesamtlösungen aus dem Akzidenzbereich auch für Verpackungsdrucker bereit. Hier ein exemplarischer Überblick der Highlights:
CTP
Wie im eigenen Unternehmen erleben die Besucher des PMC die Vorteile der Suprasetter-Belichter in einem separaten Vorstufenraum. Die Leistung eines ausgewachsenen 90 PS-Motors ist nötig, um die zwei Meter breite Belichtungstrommel im Suprasetter 145/162/190 in Bewegung zu versetzen. Mit dem voll automatischen Auto Cassette Loader belichtet der großformatige Suprasetter bis zu 35 Platten pro Stunde. Dank der integrierten Produktion liegen jederzeit alle Jobinformationen über die Anzahl der bereits belichteten Platten, beziehungsweise der belichteten Quadratmeter vor.
Druckmaschinen
Weiter gehts in den Drucksaal des PMC: Das leichte Vibrieren der Luft, verbunden mit dem typischen Brummen der produktionsbereiten Speedmaster-Maschinen unterschiedlicher Formate lässt keinen der Fachbesucher unberührt. Der Markterfolg der Speedmaster XL 105 zeigt deutlich, wie gut diese Maschine bei Verpackungs- und Akzidenzdruckern mit höchsten Qualitäts- und Produktivitätsanforderungen ankommt. Die XL 105 verarbeitet ein breites Spektrum an Substraten bei maximaler Fortdruckgeschwindigkeit von 18.000 Bogen/h. Über das Farb-/Feuchtsystem Hycolor lassen sich auch Sujets mit geringer Farbabnahme genauso stabil drucken wie solche mit hoher Flächendeckung. Kurze Waschzeiten, schnelle Farbwechsel und die kontinuierliche Materialver- und -entsorgung in Verbindung mit dem vollautomatischen Non-Stop-Anleger sind gerade für Verpackungsdrucker entscheidend. Spezialanwendungen und hochwertige Veredelungen lassen sich über die voll integrierte UV-Ausstattung, Doppellackmaschinen, Duo-Press-Konfigurationen oder das Kaltfolienmodul FoilStar realisieren.
Die Großformatmaschinen der Baureihen Speedmaster XL 145 und XL 162 basieren auf der technologischen Plattform der XL 105 und bieten somit ebenfalls die entscheidenden Vorteile schneller Rüstzeiten, Makulatureinsparungen, konstant hoher Druckqualität, hoher Flexibilität bei unterschiedlichen Bedruckstoffen und hoher Maschinenverfügbarkeit. Zusätzlich werden wichtige Faktoren im Verpackungsdruck wie beispielsweise eine hohe Anzahl von Nutzen auf einem Bogen und der hohe Durchsatz für große Auflagen realisiert. Insbesondere große Nutzen, zum Beispiel für Verpackungen in der Lebensmittel-, Elektronik- oder Spielwarenindustrie, lassen sich in den neuen Formaten effizienter produzieren. Wie schon bei der XL 105 wird höchste Maschinenproduktivität schon am Anleger sichergestellt, der mit automatischer Luft-/Geschwindigkeitskompensation, dem durch Sensoren gesteuerten Bogentransport, der Auto-Nonstop-Technologie beim Stapelwechsel und verschiedenen, auf die jeweiligen Kundenbedürfnisse zugeschnittenen Logistikvarianten, aufwartet. Hinzu kommen das simultane Waschen von Farbwerk, Gummituch und Gegendruckzylinder und der synchrone Plattenwechsel in allen Druckwerken in weniger als zwei Minuten.
Qualität zentral in der Produktion überwachen und steuern
Alles in Farbe aber stimmt die vom Printbuyer geforderte Qualität? Für die Produktion von Verpackungen zeigt Heidelberg an zentraler Stelle im Drucksaal des PMC eine Reihe von aufeinander abgestimmten Technologien in einem Gesamtkonzept zur Qualitätssicherung. Das spektralphotometrische Qualitätsmess- und -regelsystem Prinect Image Control ist die zentrale Instanz innerhalb des Farbworkflows zur Sicherstellung der Druckqualität. Die von Heidelberg entwickelten Mini Spots (kleine, intelligente Farbmessfelder) werden zur Prozesskontrolle an freien Stellen auf dem Druckbogen platziert. Sie liefern Daten über den Farbraum sowie die Tonwertzunahme auf dem Druckbogen und somit Informationen, mit deren Hilfe die Qualität über die gesamte Auflage sichergestellt werden kann. Der Prinect Color Assistant dient der automatischen Übernahme von Farbvoreinstellkennlinien aus der Vorstufe eine Funktionalität, die im Hinblick auf häufig verwendete Sonderfarben für Verpacker besonders interessant ist. Heidelberg arbeitet darüber hinaus daran, einen für den Einsatz von Sonderfarben besonders geeigneten lernenden Farbeinlauf zu entwickeln.
In der Druckmaschine ermöglicht Prinect Inpress Control die laufende Farbregelung, ohne dafür die Produktion anhalten zu müssen. Prinect Inspection Control überprüft mit zwei hochauflösenden RGB-Kameras jeden einzelnen Druckbogen auf Fehler. Das Bogen-Inspektionssystem vergleicht entweder das Druckdaten-PDF oder einen freigegebenen Bogen mit jedem gedruckten Bogen. Besonders hohe Produktionssicherheit bietet dies zum Beispiel für Hersteller von Pharmaverpackungen, die so die Fehlerfreiheit von Dosierungs- oder Einnahmeinformationen automatisch im laufenden Prozess prüfen können, bevor die Auflage weiterverarbeitet oder gar ausgeliefert wird. Und: In einer integrierten Verpackungsproduktion ist höchste, stets reproduzierbare Qualität nicht nur rentabler zu erreichen, sondern auch über die gesamte Auflage lückenlos dokumentierbar.
Mehrwert: Ausgefallene Veredlungseffekte sichern Wettbewerbsvorteile
Auch die beste Druckqualität kommt heute bei immer mehr Aufträgen nicht mehr ohne Effekte aus ausgefallene Veredlungsmöglichkeiten bringen als Differenzierungsmerkmal im Wettbewerb zusätzlichen Nutzen für Verpackungsdrucker und deren Kunden. Besondere Veredelungen bieten ein Alleinstellungsmerkmal für den Drucker im Preiskampf ebenso wie für den Printbuyer, dessen Produkte durch ihre besondere Attraktivität am Point of Sale brillieren. Heidelberg stellt dafür seine Technologien, sein Anwendungs-Know-how und seine Expertise im Sondermaschinenbau zur Verfügung allesamt fließen in Veredlungslösungen, mit denen sich Akzidenz- wie Verpackungsdrucker durch nicht alltägliche Produkte im Markt abheben können.
Wie sich höchste Produktivität mit außergewöhnlichen Druckergebnissen verbinden lässt, zeigt im PMC beispielsweise eine Heidelberg Speedmaster XL 105 Duo, eine Offset-Druckmaschine mit integriertem Flexowerk. Ob Flexo vor Offset oder umgekehrt über die konsequente Weiterentwicklung des Lackierwerks zum Flexowerk lässt sich zum Beispiel ein sattes Weiß erzielen, das sich noch im selben Durchgang weiter bedrucken lässt. Mit der Duo-Maschine aufgetragene Iriodin-, Silber- oder Gold-Lacke bewirken etwa auf dunklen Flächen besondere Glanzeffekte. Auch die FoilStar-Technologie weiß beim Publikum zu punkten: Die PMC-Besucher sehen Etiketten und Verpackungen, bei denen Kaltfolie mit UV-Lack oder Kaltfolie und konventionelle Druckfarben zum Einsatz kommen und loben die Brillanz der erzielten Effekte. FoilStar wird auf ein konventionelles Druckwerk aufgesetzt und kann bei Bedarf abgeschaltet werden mit wenigen Handgriffen lässt sich das Druckwerk wieder für den normalen Offsetdruck verwenden.
Weiterverarbeitung
Go with the Workflow dem idealen Materialfluss entsprechend folgt in den Präsentationen im PMC direkt im Anschluss an die Druckmaschinen die Weiterverarbeitung. Die Stanzen von Heidelberg wie die Dymatrix 106 CSB Pro arbeiten nach dem Prinzip des bewegten Obertischs, das mit wenigen Haltepunkten einen horizontalen und besonders materialschonenden Bogentransport ermöglicht. Dies trägt zur hohen Qualität einer Verpackung bei und sichert den Markterfolg. Zusätzlich ermöglicht das patentierte Registersystem in jeder Station höchste Präzision beim Stanzen, Ausbrechen und bei der Nutzentrennung. Typisch für Heidelberg sind das ergonomische Gesamtkonzept und die Touchscreen-Bedienung nach bekanntem Heidelberg Standard, um nur einige der Vorteile zu nennen.
Die Faltschachtelklebemaschine Diana X 115 ist modular konstruiert und kann daher bei steigen Anforderungen mitwachsen. Damit bleiben einerseits bereits getätigte Investitionen rentabel, und andererseits lässt sich die Maschine für spezifische Anforderungen konfigurieren, so dass Produkte möglich werden, die wiederum zur Differenzierung und damit zum Erfolg im Wettbewerb beitragen. Mit dem optionalen Diana Feeder und Diana Packer kann die Maschine bis zu 200.000 Faltschachteln pro Stunde produzieren. Fehlerhafte Schachteln werden automatisch erkannt und ausgeschleust, die Qualität der Auflage bleibt auf höchstem Niveau.