Drucksaal
Unfold your Potential: Doppelte Produktivität im Akzidenzdruck mit Push to Stop end-to-end
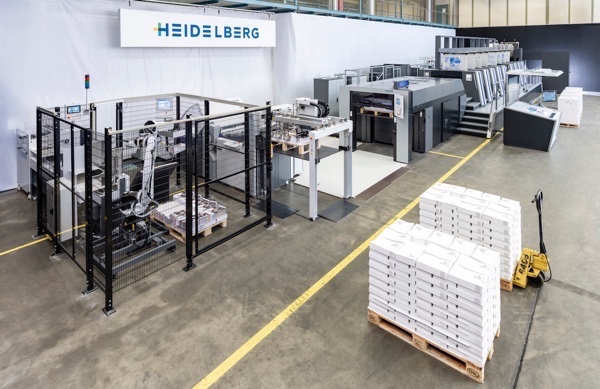
Dienstag 20. Oktober 2020 - Welche Lösungen benötigen Akzidenzdrucker, um im Markt wettbewerbsfähig und profitabel zu sein? An welchen Prozessen und Schnittstellen können noch Potenziale gehoben, und wie können die Mitarbeiter der Druckereien noch besser unterstützt werden?
Diesen Fragen stellten sich die Experten der Heidelberger Druckmaschinen AG (Heidelberg) bei der Entwicklung von aktuellen Innovationen. Die Antworten werden die Produktivität der Branche auf ein neues Niveau heben: Für hochindustrialisierte Akzidenzdruckereien mit standardisierten Abläufen zeigt Heidelberg erstmalig die autonome Produktion von der Dateneingabe bis zur gefalzten Signatur – Push to Stop – end-to-end.
Mit seinem breit angelegten, skalierbaren Funktionsumfang organisiert der Produktions-Workflow Prinect Production Manager die digitalisierten Prozesse im Smart Print Shop. Er sorgt für schlanke kosteneffiziente Abläufe und Wachstumspotenzial auch in den kleineren und mittelgroßen Betrieben. Über das Prinect Digital Front End (DFE) integriert er nicht nur Offset- sondern auch Digitaldruckmaschinen.
Mit dem Digital Cluster-Produktionsmodus gibt es eine neue Funktionalität im Prinect DFE.
Damit können mehrere Versafire der neuen Generation unter einer gemeinsamen Job-Queue betrieben und somit die optimale Verteilung der Aufträge organisiert werden.
Alles ganz von selbst – völlig autonome Produktion inklusive Weiterverarbeitung wird real
Mitte Oktober zeigte Heidelberg bei einer Präsenz-Veranstaltung am Standort Wiesloch-Walldorf als Weltpremiere die völlig autonome Produktion. Das leistungsstarke digitale Planungssystem Prinect Scheduler plant die eingehenden Daten in einer optimalen Reihenfolge nach Kriterien wie Papier, Farbbelegung und Falzschema. Die Belichtung der Druckplatten erfolgt vollautomatisch über die Suprasetter Produktionslinie in der richtigen Reihenfolge. „Prinect weiß zu jeder Zeit, welche Platten auf welchem Plattenspeicher abgelegt sind. Die Reihenfolge der Jobs auf dem Plattenspeicher ist optimiert, so dass von Job zu Job nur möglichst kleine Veränderungen stattfinden – wir nennen das inkrementelles Rüsten. Basierend auf Bedruckstoffparametern und Auftragsdaten kann die zu erwartende Papierdehnung kalkuliert und schon bei der Belichtung kompensiert werden. Das spart Zeit und Makulatur“, erklärt Rainer Wolf, Leiter Segmentmanagement Commercial bei Heidelberg.
Direkt vom Prinect Scheduler werden die Aufträge automatisch in den Auftragsspeicher der Druckmaschine geladen. Dies inklusive der Information zum dazugehörigen Plattenspeicher. Mit Plate to Unit, der neuen vollautomatischen Druckplattenlogistik an der Druckmaschine, erfolgt die Bereitstellung der Druckplatten und deren Entsorgung komplett automatisiert. „Bei industrieller Produktion von Kleinauflagen kommen wir schnell auf zehn bis zwanzig Auftragswechsel pro Stunde. Plate to Unit entlastet den Bediener und sorgt für einen sicheren, stabilen Prozess. Jede Platte hat eine individuelle ID. So stellen wir sicher, dass die richtige Platte zur richtigen Zeit im richtigen Druckwerk bereitgestellt wird. Das Risiko von Knicken oder Kratzern auf der Platte ist ausgeschlossen. Der Prozess ist stabiler, Ausfallzeiten sind minimiert und die Qualität ist besser“, freut sich Rainer Wolf.
Die Speedmaster XL 106-8+P+L der Generation 2020 bringt alles mit, um die Leistungsfähigkeit der Maschine systematisch nutzbar zu machen. Die Bedienernavigation erreicht ein neues Level mit weiteren intelligenten Assistenzsystemen und der Nutzung von künstlicher Intelligenz. Die neue Heidelberg UX schafft so ein neues Nutzererlebnis und einen modernen Arbeitsplatz, der höchste Performance ergonomisch unterstützt. So organisiert und optimiert die patentierte Software Intellistart 3 die Rüstprozesse. Die neue Software Intellirun erweitert die Navigationsfunktionalität über den Rüstprozess hinaus. Situationsgesteuert gibt sie dem Bediener laufend Hinweise, welche Aktivitäten erforderlich sind, um unnötige Hilfszeiten zu vermeiden. So wechselt der Wallscreen XL rechtzeitig vor Erreichen der Auflage ins Menü der Auftragsvorbereitung. Der Bediener kann die Daten rechtzeitig überprüfen, sich mit der anstehenden Wechselsequenz vertraut machen und eventuell noch fehlendes Material bereitstellen. Solche Navigationsfunktionen werden immer wichtiger. Am Wallscreen XL sorgt die Zeitstrahldarstellung Intelliguide für Transparenz über alle Prozesse. Der Bediener sieht genau, wann manuelle Eingriffe erforderlich sind. Die Bedienernavigation erfolgt jedoch nicht nur am Maschinenleitstand, sondern kommt nun mit dem neuen Intelliline auch an die Druckwerke der Maschine. LED-Leisten zeigen, ob die Maschine produziert, rüstet oder ob und wo Aktionen des Bedieners erforderlich sind. Mit der Press Center Mobile App werden Leitstands-Informationen auch mobil bereitgestellt. Der Bediener hat die Auftragsdaten und den Maschinenstatus immer in Echtzeit verfügbar und kann diese beispielsweise bei der Bereitstellung von Materialien für den Folgeauftrag nutzen.
Um mit einem makulaturfreien Stapel in die Weiterverarbeitung zu gehen, wurde erstmals die Makulaturweiche an einer Wendemaschine integriert. Die Maschine erkennt Makulaturbogen und schleußt diese automatisch aus. Die ausgeschleusten Bogen werden sofort geschreddert und über eine Absauganlage entsorgt. Das Entleeren eines Auffangbehälters entfällt.
Immer kürzere Lieferzeiten erfordern, dass die Bogen möglichst schnell in die Weiterverarbeitung gelangen. Die neue Generation der DryStar LED Pro Trocknersysteme ist nicht nur 20 Prozent leichter, sie ist zudem noch leistungsfähiger und sorgt für einen trockenen Stapel in der Auslage, der sofort weiterverarbeitet werden kann.
Dieser wird dann mit einem bedienerlosen Transportsystem an die Falzmaschine Stahlfolder KH 82-P gefahren, die mit dem unterschuppten Falzprinzip zirka 15.000 Bogen in der Stunde falzt. Die KH 82-P ist ebenfalls über das Push to Stop-Konzept integriert und erkennt die nächste Signatur automatisch am mitgedruckten Barcode. Jede neue Signatur wird eigenständig erkannt und automatisch gestartet. Gegenüber den bisherigen Abläufen können hier insgesamt sechs Arbeitsschritte eingespart und der Bedienereinfluss ausgeschlossen werden. „Zirka sieben Tonnen Papier setzt der Bediener bei dieser Hochleistungsmaschine in einer Schicht ab – alle zwölf Sekunden ein Päckchen. Nur wenn es uns gelingt, ihn hierbei signifikant zu entlasten, kann das volle Potenzial der Maschine konstant realisiert werden. Genau hierfür haben wir mit den Stahlfolder P-Stacker als industrielle Robotiklösung entwickelt, die auch die Nutzung von Europaletten zulässt. Das meiste Know-how liegt hierbei im ausgeklügelten Greifersystem, das der menschlichen Hand nachempfunden wurde“, erklärt Rainer Wolf. Der Bediener an der Falzmaschine wird signifikant entlastet und erhält einen modernen, automatisierten und hochproduktiven Arbeitsplatz.
Eine weitere Weltpremiere im Bereich Falzmaschinen ist der Stahlfolder TH 56 Pharma, der mit umfangreicher Automatisierung und robuster Maschinenplattform eine neue Leistungsklasse im Wachstumsfeld Pharma definiert. Mit vielen neuen Extras lassen sich vielfältigste Packungsbeileger wesentlich wirtschaftlicher herstellen, wie auf den aktuell vorherrschenden manuell einzustellenden Falzmaschinen.
Auch beim Schneiden an den Polar-Schneideanlagen gibt es neue Push to Stop-Lösungen. War bisher das Rütteln ein arbeitsintensiver manueller Prozess, wird dieser nun mit dem neuen AirGo Jog-System komplett automatisiert.
„Wir sprechen provokativ davon, mit Push to Stop – end to end die Produktivität zu verdoppeln. Das ist jedoch für die Mehrzahl der Druckereien durchaus möglich – einige wenige machen es schon in der Praxis vor und das sind nicht nur die Web to Print-Drucker. Es ist uns ein Anliegen, dass wir unsere Kunden in die Lage versetzen, diese Potenziale zu erschließen. Denn der Erfolg unserer Kunden ist letztlich auch unser Erfolg,“ erklärt Rainer Wolf.
Smart Print Shop setzt hohe Flexibilität und mehr Profit in mittelständischen Druckereien um
Bei der Veranstaltung zeigte Heidelberg zudem, dass der Smart Print Shop auch für kleinere und mittlere Druckereien die Lösung ist, um wirtschaftlich zu produzieren und im immer härter werdenden Wettbewerb bestehen zu können. „Weniger Überstunden und Sonderschichten, sowie mehr Zeit, um sich um die Kundenbindung zu kümmern, dazu Transparenz zu haben, welche Aufträge profitabel waren und welche nicht. All das sind Vorteile, die der Smart Print Shop mitbringt und die auch für kleinere Betriebe wichtig sind. Die produzierten Volumina sind dort jedoch geringer und vielfältiger. Sie erfordert entsprechend andere Produkte, die in das Budget passen. Hier haben wir mit unserem breiten Portfolio einiges zu bieten. Von skalierbaren Softwarelösungen über Push to Stop-Funktionalität an allen Druckmaschinen, bis hin zu entsprechenden Lösungen in der Weiterverarbeitung“, bestätigt Rainer Wolf.
Das komplett neu überarbeitete Prinect Press Center Generation 2020 mit dem neuen Speedmaster Operating System bringt Push to Stop-Funktionalität und die Prinect Cloudschnittstelle an jede Speedmaster – von der SX 52 bis zur XL 106. An den beiden Speedmaster CX 75 und XL 75 erlebten die Besucher, wie mit den vielen neuen Assistenz-systemen das Prinect Press Center zum modernen, attraktiven Arbeitsplatz wird. Mit der Heidelberg UX wird der Bediener in die Lage versetzt, das Leistungspotenzial der Maschine kontinuierlich abzurufen. Mit diesen digitalisierten und automatisierten Prozessen wird das navigierte Drucken umgesetzt – bis hin zur Weiterverarbeitung an der Falzmaschine Stahlfolder KH 82, die ebenfalls in das Push to Stop-Konzept integriert ist.
Mittelständische Druckereien zeichnen sich durch ein breites Angebotsportfolio aus und produzieren dieses sowohl im Offset- als auch im Digitaldruck . Als Digitaldrucksystem bietet Heidelberg mit der Versafire ein digitales Bogendrucksystem an, das über das Prinect DFE in die gesamten Druckprozesse integriert ist.
Durch diese enge Integration von Offset- und Digitaldruck kann der Kunde noch bis kurz vor dem Druckstart festlegen, welches Druckverfahren für den speziellen Auftrag und der aktuellen Auslastungssituation am wirtschaftlichsten ist. Auch kleine Auflagen, die vorher im Offset hergestellt wurden, können reibungslos im Digitaldruck nachproduziert werden. Die Bediener kennen den Ablauf des Workflows und müssen sich weder spezialisieren noch umstellen. Fehlerquellen werden minimiert, die Flexibilität und die Profitabilität steigen.
Durch das bewährte Heidelberg Color Management wird der Farbraum der Versafire so genutzt, dass das Ergebnis am besten mit dem im Offset bedruckten Bogen abgestimmt ist. Die Rastertechnologie ist identisch. Dadurch lassen sich auch Hybridproduktionen umsetzen, wie beispielsweise der Druck eines individualisierten und personalisierten Titels im Digitaldruck und Produktion der Inhaltsseiten über Offset, oder auch Offset-Vordruckbögen mit der Versafire in das Endprodukt einbinden.
Für Druckereien, die ein hohes Volumen an Digitaldruckaufträgen abarbeiten, hat Heidelberg mit dem neuen Digital Cluster-Produktionsmodus eine weitere Funktionalität für das Prinect DFE entwickelt. Dabei handelt es sich um ein smartes Jobmanagement in einem produktiven Cluster, das aus zwei oder mehreren Versafire besteht, die über das Prinect DFE verbunden sind.
Der Digital Cluster-Produktionsmodus ist eine skalierbare Lösung mit geringem Investitionsaufwand, um das digitale Produktionsvolumen zu einem günstigen Preis-Leistungs-Verhältnis zu steigern.
Die Versafire steht für Verlässlichkeit und Qualität. Über das integrierte Media Management Tool erfolgt eine automatische Einstellung von über 200 Maschinenparametern, um das perfekte Druckbild auf einer Vielzahl von Substraten zu erreichen. Für spezielle Bedruckstoffe können diese Parameter zudem feinjustiert werden, beispielsweise wenn der Endkunde ein spezielles Papier wünscht. Die Versafire verarbeitet die unterschiedlichsten Substrate, wie synthetische, strukturierte, metallisierte, oder im Offset vorgedruckte Materialien, bis hin zum Sonderformat mit bis zu 1.260 mm oder personalisierte Verpackungen in Kleinauflagen. „Die Versafire bietet den Druckereien ein breites Produktportfolio, eine flexible Anpassung und Erweiterung ihres Druckjobangebots und somit neue Geschäftsmodelle und das bei einem attraktiven Preis-Leistungs-Verhältnis insbesondere im Vergleich zu Flüssigtoner oder Inkjet-Systemen“, fasst Rainer Wolf zusammen. „Über 1.600 Installationen belegen den Erfolg der Versafire im professionellen Druckumfeld. Sie ist aus unserem Portfolio nicht mehr wegzudenken und ein wachsender Bereich, den wir weiter ausbauen werden.“