Workflow
Blair Labeling profitiert von den Automatisierungsvorteilen der Automation Engine QuickStart von Esko
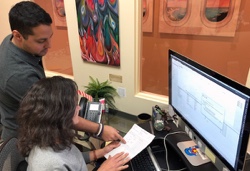
Freitag 08. Dezember 2017 - Die Installation eines effektiven Workflows muss nicht schwierig sein. Innerhalb von nur einer Woche hat die in Denver, USA, ansässige Druckerei Blair Labeling, Inc. (www.blairlabeling.com) die Software Automation Engine QuickStart for Labels von Esko (www.esko.com) installiert. Damit war das Unternehmen in der Lage, den manuellen Arbeitsaufwand für seine fünf Flexodruckmaschinen und die neue Digitaldruckmaschine in der Druckvorstufe um mehr als 30 % zu verringern.
Blair Labeling, Inc. (Blair) befindet sich zu einhundert Prozent im Besitz von weiblichen Angehörigen ethnischer Minderheiten. Seit 1986 produziert die Druckerei mehrfarbige Premium-, Werbe- und industrielle Selbstklebeetiketten sowie Aufkleber, manipulationssichere Etiketten, Thermo-Etiketten, Muster, Anhänger, Laschen und Karten. Die 20 Mitarbeiter stehen nicht nur an den Druckmaschinen, sondern kümmern sich auch um das Schneiden, Perforieren, Stanzen, Laminieren/UV-Beschichten und um Rasterfolien – natürlich alles inline. Daneben betreibt Blair eine Full-Service-Grafikabteilung für Entwürfe und Druckvorstufenleistungen.
Noch vor wenigen Jahren hat Blair mit einem Workflow-System gearbeitet, das sehr schwer zu bedienen war. „Beim kundenspezifischen Über-/Unterfüllen, mussten wir beispielsweise das Distanztrapping auf der weißen Unterschicht von Hand herstellen. Es war ein Alptraum“, erinnert sich Marco De La Vega, CFO von Blair. Dann gingen sie langsam zu den Produkten von Esko über. „Wir arbeiteten gern mit Esko, da die Tools in Adobe Illustrator integriert und keine separaten Programme waren. Nachdem wir einige Erfahrung gesammelt hatten, wollten wir die Druckvorstufe automatisieren und beschlossen, in Automation Engine QuickStart zu investieren. Diese vorkonfigurierte und mühelos zu nutzende Workflow-Lösung geht die wichtigsten Herausforderungen an, die sonst den Durchsatz und die Effizienz der Etikettenproduktion beeinträchtigen. Sie übernimmt solche Arbeiten, wie den Preflight für Verpackungen, das Prüfen von Barcodes mit zusätzlicher Ausgabe von Qualitätsberichten, Über-/Unterfüllen, Step-and-Repeat, das Einfügen intelligenter Markierungen und Kontrollstreifen sowie das Erstellen von Berichten.
„Die Integration verlief nahtlos, wahrscheinlich eine der einfachsten, mit der ich jemals zu tun hatte – und ich habe schon eine Menge gemacht“, sagt De La Vega. „Ich dachte, wir würden Monate brauchen, um das alles einzurichten. Sogar eine Fremdfirma hatte ich angerufen, damit sie sich bereithält, falls wir im Notfall ihre Hilfe brauchten. Das war aber überhaupt nicht nötig. Innerhalb von einer Woche war die gesamte Software installiert und die Produktion voll angelaufen.“
„Eine Woche vor der Installation hatte ich mit Esko darüber gesprochen, wie unsere Prozesse ablaufen. Esko hat ihn nicht in Frage gestellt und auch die Benennungsregeln nicht geändert. Sie sind einfach gekommen und haben Automation Engine QuickStart so konfiguriert, wie wir die Druckerei führen“, betont De La Vega. Esko hat den Workflow installiert sowie die spezifischen Parameter, Datenbank-Abfragen und intelligenten Markierungen eingerichtet, die Blair benötigte. Anschließend erhielten De La Vega und seine Grafikerin eine Schulung zu Bedienung der vorkonfigurierten Workflows. Innerhalb von nur einem Tag hat De La Vega das System bereits beherrscht.
Jetzt arbeitet Blair seit etwa drei Monaten mit Automation Engine QuickStart. „Eines der Hauptprobleme, die wir davor hatten, betraf das Management der Produkte. Mir gefällt besonders, dass ich heute die Produktdatenbank durchsuchen und sie als Referenz – nicht nur für Grafiken – nutzen kann. Die Software erlaubt mir, Produkte mühelos nach einem Schlüsselwort auf dem Etikett suchen zu lassen. Das ist unglaublich. Das System erfasst einfach alles. Wir finden das Jobticket vom letzten Auftrag, das uns zeigt, ob es Änderungen gegeben hat. So arbeiten wir immer mit der aktuellen Produktversion. Zum Beispiel haben wir einen Kunden, der das gleiche Produkt mit unterschiedlichen Nährwertangaben vertreibt. Dieser Auftrag war sehr fehleranfällig, weil schwer war zu erkennen, welche Angaben im jeweiligen Fall zu verwenden waren. Heute zeigt mir das System den richtigen Proof und alle freigegebenen Änderungen am Text genau an.“
Auch war De La Vega auf der Suche nach einem System, das sich kinderleicht bedienen ließ. „Es ist beeindruckend, dass 98 % aller Aufträge automatisch verarbeitet werden. Die manuelle Arbeit ist auf 2 % der Aufträge mit komplizierten Arbeitsschritten beschränkt. Diese würden wir aber sowieso nicht automatisieren wollen“, ergänzt De La Vega. „Unsere Druckvorstufen-Grafikerin ist sehr kompetent und löst die meisten Probleme ohne fremde Hilfe. Ich bin froh, dass wir keinen Workflow-Spezialisten benötigen.“
In der Tat hat Automation Engine QuickStart einen Grafiker eingespart. „Vorher war ich an den Grafiken aller Kunden beteiligt und habe 30 % der Arbeit erledigt. Unsere Grafikerin hat 70 % übernommen“, sagt De La Vega. „Jetzt muss ich gar nicht mehr mithelfen. Sie hat alles im Griff und fragt sogar, ob sie noch mehr übernehmen soll.“
Im Durchschnitt verarbeitet Blair etwa 20-25 Einzelaufträge pro Tag, wobei jeder Auftrag drei bis vier Grafiken enthält. Seitdem sie etwa zu der Zeit, als der Esko Workflow installiert wurde, in eine Digitaldruckmaschine investiert haben, hat sich die Anzahl der Aufträge zwar nicht erhöht, aber sie sind mit mehr Kunden zum Digitaldruck gewechselt, um die Nachfrage beim Flexodruck erfüllen zu können. „Die Auflagenhöhe pro Auftrag hat sich erhöht. Pro Stanzform werden etwa 20 bis 35 Grafiken digital ausgeführt“, sagt De La Vega. „Allerdings verzeichneten wir im vergangen Jahr ein Wachstum von 6 %, während sich die Plattenherstellung wegen der Digitaldruckmaschine um 10 % verringert hat. Daher gehen wir von einem weiteren Wachstum bei gleichzeitigen Kosteneinsparungen aus. Wir wählen mehrere Grafiken aus und das System übernimmt die Anordnung. Früher war der Zeitaufwand in der Druckvorstufe viel größer. Diesen Fortschritt führe ich auf die effizienzsteigernden Maßnahmen in der Druckvorstufe sowie darauf zurück, dass wir jetzt viel mehr Aufträge auf der Digitaldruckmaschine erledigen.“
Dort druckt Blair Wasserflaschen-Etiketten einer Handelsmarke für ein Unternehmen, das innerhalb von zwei Monaten 86 verschiedene Produkte benötigte. Blair fasst die Produkte zu Sammeldrucken zusammen und produziert verschiedene Etiketten gleichzeitig. „So sparen wir viel Zeit. Wir drucken fünf verschiedene Etiketten, von denen die gleiche Anzahl benötigt wird, über die Breite und zwei über die Länge des Bogens“, erläutert De La Vega. „Vorher konnten wir immer nur Etiketten des gleichen Produkts herstellen. Selbst bei einer Entwicklungszeit von nur 15 Minuten pro Datei, ergibt sich in der Summe ein erheblicher Zeitaufwand. Das neue System hilft uns, wettbewerbsfähig zu bleiben, und es stellt sicher, dass die Kosten den Grafikaufwand decken.“
Auch konnte Blair viele der üblichen Bedienerfehler vermeiden. „Das System macht genau das, was der Bediener möchte. Es gibt die gewünschte Arbeit aus und zeigt sie ihm. Früher habe ich beim Step-and-Repeat manchmal den falschen Text ausgewählt. Jetzt zeigt das System die richtigen Parameter mit der richtigen Grafik an, die dann auch einwandfrei gedruckt wird“, sagt De La Vega.
„Die Automatisierung hat uns geholfen, sehr produktiv zu werden. Dabei war der Wechsel ganz einfach. Je besser wir Automation Engine QuickStart beherrschen, desto schneller werden wir wachsen und neue Funktionen umsetzen“, ergänzt De La Vega abschließend. „Noch einmal vor die gleiche Entscheidung gestellt, würde ich Automation Engine QuickStart auf jeden Fall wieder installieren und sogar meinen Job darauf verwetten, dass es zuverlässig funktioniert. Ich bin mir sicher, dass es nichts gibt, was das System nicht kann.“